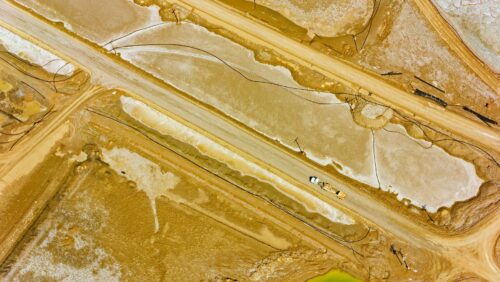
How We Can Eliminate the Need for Mined Minerals by 2050
Battery circularity strengthens the EV battery supply chain, improves its efficiency, bolsters the economy, and increases energy independence.
As demand for EV batteries grows rapidly, the United States must ensure a responsible, resilient supply chain is in place to meet this demand.
Today’s linear supply chain relies on newly mined minerals, the extraction of which is associated with social and environmental harms. Furthermore, just a few countries dominate the supply chain, making it vulnerable to changing geopolitics and trade alliances.
A circular battery economy — one in which end-of-life (EOL) batteries are reused, repurposed, or recycled — can help address these issues. Powering the Future: Overcoming Battery Supply-Chain Challenges with Circularity, a new report by RMI, the World Economic Forum, and Global Battery Alliance, reveals how a circular battery economy can help minimize batteries’ social and environmental impacts and enable a widespread transition to EVs by reducing supply gaps and strengthening the supply chain. It can also decrease geopolitical tensions by reducing competition for resources, increase geopolitical and economic standing for countries that are able to take on a bigger role in the supply chain, and expand access to clean energy and clean mobility.
To fully leverage these opportunities, the United States needs to fundamentally shift how we think about the supply chain.
Below, we outline three approaches that can help us realize the benefits of a circular battery economy. We also describe how RMI’s free, user-interactive Battery Circular Economy Initiative (BCEI) Dashboards can help EV battery (EVB) stakeholders make informed decisions to get us there.
1. Get the most out of mined minerals.
It will take some time to build the infrastructure to support a robust circular battery economy, so in the short term we will need to continue mining to meet growing demand for batteries. But by focusing on how to get the most out of these minerals, we can greatly reduce our need for mining. This can be done by implementing the six strategies outlined in our report, The Battery Mineral Loop: The Path From Extraction To Circularity:
- Shift to new battery chemistries: Deploy different battery chemistries that require fewer critical minerals.
- Increase energy density: Store more energy per kilogram through better battery engineering.
- Employ battery recycling: Ensure all batteries are recycled at end of life so their materials can be used in new batteries.
- Reuse EVBs and extend their lifetime: Use and reuse batteries longer to avoid the need for frequent replacements and provide a greater flow of service from a smaller stock of batteries and their minerals.
- Increase vehicle efficiency: Make cars more efficient — lighter weight, sleeker, and with better tires and accessories — and right size them for purpose to allow for smaller batteries for the same vehicle range.
- Change mobility patterns: Reduce the demand for motorized transportation and induce mode-shifts to public transit, electric micromobility, cycling, and walking through better urban planning, smarter transportation infrastructure investments, and logistics efficiency.
These strategies will not only help meet near-term EVB demand but can actually eliminate our need for new minerals by 2050.
People often say that critical minerals are the new oil — meaning that critical minerals will power our future, drive our global economy, and require ever-increasing extraction the way that oil has done in the past. This also implies that the drive to maintain strategic access to them will lead to the same geopolitical conflict and environmental impacts as oil. This concept misses a key point: minerals only need to be extracted once, while oil needs continuous extraction.
If we employ all six solutions mentioned above, we’ll only need to mine a cumulative 125 million tons of battery minerals to reach mineral self-sufficiency. This may seem like a lot, but it is 17 times smaller than the amount of oil we extract and process for road transport every year. And, at today’s commodity prices, it’s about 20 times cheaper.
To better understand how we can reach net-zero mineral extraction, stakeholders can use RMI’s new Battery Mineral Loop Dashboard to explore these six strategies and their impact on global demand for lithium, nickel, and cobalt. The dashboard allows users to adjust battery demand, innovation, efficiency, and recycling inputs to see how these parameters impact mineral demand and to better understand what levers can have the most impact in driving us toward net-zero mineral extraction.
2. Implement policies and market-based solutions to account for the true return on investment of battery recycling.
The economics of EVB recycling are challenging. High capital requirements, the need for significant feedstock (at a time when most of the available battery recycling material is production scrap), and a volatile critical minerals market can result in a low return on investment (ROI) on recycling infrastructure. However, when evaluated using a triple-bottom-line accounting approach, one that considers social, environmental, and financial impacts, EVB recycling’s ROI is greater than that of mining.
To fully capture the true ROI of battery recycling in comparison to mining, RMI assessed the system-level benefits of each, assigning a monetary value to five environmental and socioeconomic impacts: carbon emissions, water use, land use, wages earned, and GDP growth. When these externalities are accounted for, recycled minerals have a much higher ROI than newly mined minerals. However, in today’s market, these externalities are not priced into the system, so newly mined minerals are less expensive than they should be.
To rectify this and appropriately value recycling, we need policy interventions, innovative finance mechanisms, and market-based solutions that create a demand signal for recycled material.
To explore the findings of our analysis, our new, interactive Battery Recycling Economics Dashboard allows users to examine the profitability of battery recycling for four battery chemistries under different conditions by adjusting inputs such as feedstock acquisition costs, recycling plant capacity utilization, metal prices, policy-driven incentives, and EOL battery projections.
3. Invest in domestic EVB recycling and midstream manufacturing to strengthen the supply chain’s resilience, increase energy security, and boost the economy.
As our Battery Mineral Loop report notes, domestic and global demand for lithium-ion batteries — and the resulting demand for the minerals that go into them — is growing rapidly. Given that North America is not a major producer of some minerals (like cobalt, manganese, and graphite), the United States will need to rely on imports for these minerals to meet demand. At the same time, there will be a considerable increase in EVBs reaching end of life in the United States in the 2030s. If recycled domestically, these EOL batteries can help meet supply gaps and reduce our reliance on imports, which are subject to increased competition from growing global demand, volatile mineral prices, changing trade alliances, and disruptions from evolving geopolitics. By strengthening domestic EVB recycling and midstream manufacturing, we will strengthen our supply chain’s resilience and increase our energy security and independence.
To capitalize on this opportunity, the United States must ensure not only that batteries are recycled when they reach end of life, but also that we can make use of those recycled materials. The United States currently lacks capacity in the midstream portion of the supply chain, which involves refining and processing raw materials to create cathode and anode active battery materials. While it’s important that we invest in all portions of the supply chain, we need to pay particular attention to shoring up the US midstream; otherwise, recycled materials must be exported to countries with these capabilities — limiting our ability to realize the full benefits of EVB recycling in the United States.
In addition to strengthening our supply chain resilience and increasing our energy security, increased investment in recycling will create jobs. A January 2025 report from the International Council on Clean Transportation (ICCT) found that “production of battery cell components and battery recycling could generate significant employment opportunities” — including 17 jobs directly created per gigawatt-hour of batteries recycled. Furthermore, increasing domestic recycling, cell component production, and battery manufacturing simultaneously — in other words, investing in the growth of the entire domestic EVB supply chain — has the potential to create between 84,000 and 125,000 jobs in the United States in 2032, according to the ICCT report.
In our US Supply Chain Dashboard, stakeholders can enter their own battery demand scenarios and parameters for battery circularity such as battery life, collection efficiency, recycling capacity, and recovery rates, to see how these factors affect our domestic supply chain — including what supply gaps will materialize, how recycled content can help meet these gaps, and the financial value of materials recovered from recycling.
Access to information can help make a circular battery economy a reality
If the United States continues to rely on a linear EVB supply chain, we’ll miss out on battery circularity’s many social, environmental, and economic benefits. By adopting the approaches outlined above, the country can hasten instead of impede the transition to electrified transportation, while reducing negative impacts and risks in the supply chain, increasing our energy independence and security, and boosting our economy.
We need concerted, coordinated effort by stakeholders across the value chain to implement these solutions. RMI’s Battery Circular Economy Initiative Dashboards can help provide the information they need to make data-driven decisions to make a circular battery economy a reality.
Explore the three Battery Circular Economy Initiative Dashboards here.